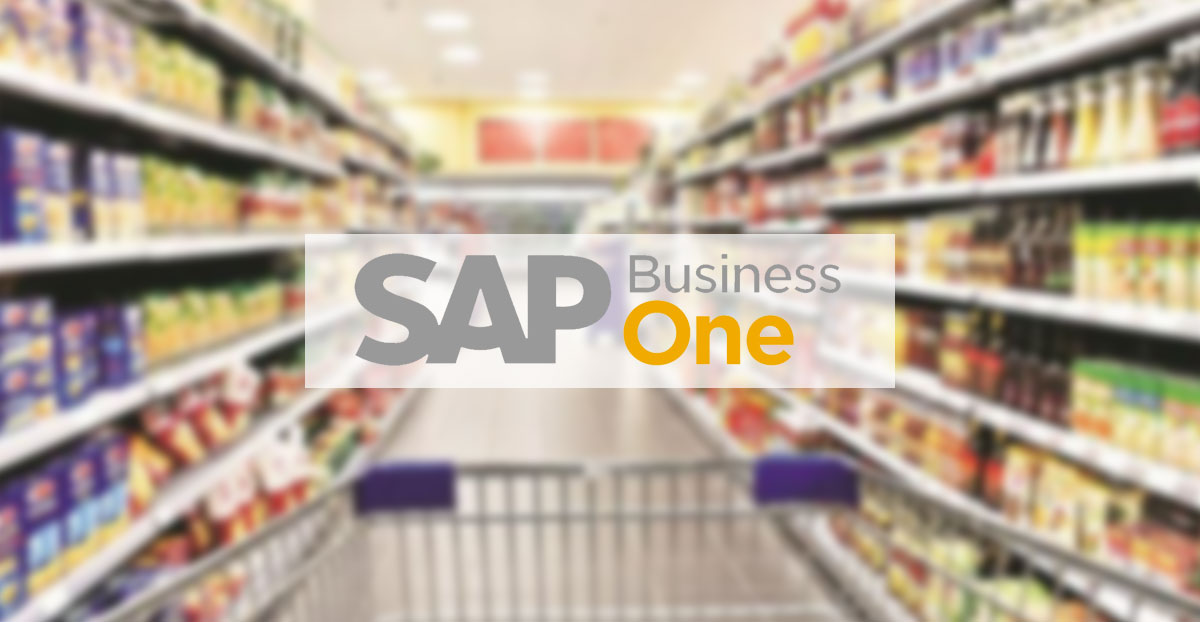
Fast Moving Consumer Goods or FMCG is an industry that caters to the everyday needs which includes an array of products that include daily supplies.
The turnaround time is very quick in an industry like this and there are a lot of processes that work as a chain and it is necessary to maintain a smooth flow of these functions to ensure timely delivery of the products.
Enterprise Resource Planning (ERP) is an integrated set of subsystems that integrates all facets of the business, including planning, manufacturing and logistics, sales and marketing.
ERP systems are originated to serve the information needs of manufacturing companies.Over time though, they have grown to serve other industries, including financial services, customer good sector, supplier chain management and human resource sector.
FMCG enterprise requires consolidating their information base that’s been accumulated from different sources. As the company has operations spread across a wide area, the major problem is data integration. The company had deployed ERP systems to optimise the distribution network and improve delivery mechanisms. Implementing ERP solutions has led to an improvement in the service levels of the organization vis-à-vis their dealers, through the redressal of potential stock-out situations. This has also been made possible due to better visibility of sales, inventory and production in progress data.
SAP Business One Key features for FMCG
- Inventory Management System
- Material Requirement planning
- Production and Capacity planning
- Delivery Schedule management
- Bill of Materials Management
- Procurement and Order management
- Costing and Quality Management
- Multiple Warehouse Management with Barcode
SAP Business One Benefits for FMCG Industry
- Improves the supply chain management process.
- Improves operational efficiency.
- Quality control and management
- Recipe and ingredient management
- Raw materials, spares procurement through MRP (Material Requirements Planning).
- Lot tracking and traceability.
- Monitoring and tracking – Product-wise and unit-wise monitoring and tracking of WIP in real-time give clear visibility into the status of daily-target Vs actual-progress.
- Plant Maintenance – The robust plant maintenance module’s preventive maintenance, predictive maintenance, and breakdown maintenance provisions through automated periodical notifications ensure the maximum efficiency of machine usage and minimization of downtime.
- Finance & Costing – The system aids the accurate calculation of the manufacturing cost of any FMCG by closely monitoring the actual material consumed, machine usage, manpower, and overheads.
- Reports and Dashboard – Dashboards help to track the Level of Stock in warehouses across geographical borders and multiple customized reports for management and employee.